John P.
AH enthusiast
The beast, about 2000 pounds. One station for the pattern stock and two stations for carving. The far right position is equipped with a reversing mechanism allowing a left hand stock to be carved from a right hand pattern or vice versa. Or disconnect the reverse mechanism and carve two identical stocks. This NorthStar is unique in that the carriage runs on linear bearings instead of the usual drum and cable arrangement (Most North Star Duplicators are cable and drum). Despite the weight of the heavy carriage the machine is easy to operate and very precise. All that weight and structural mass makes for an accurate machine. My obtaining this machine is an interesting story which I will tell at a later date.
Back view. That funny looking knob on the back of the tracing arm is an adjustable balance weight on a length of 1" all thread. Those big 220 volt motors have a lot of torque.
The blank is Pacific Big Leaf Maple with a 21 year air cure. 2-3/4" thick as the stock will have 3/8" cast off. The pattern is made from plain grain maple and painted with hard black epoxy paint for a slick tracing surface.
First thing is to layout the location for the duplicator centers. The rear is a spur center, front is a cupped center.
Center lines and a 3/8" offset for the cast off. The pattern was made with 3/8 cast off. Blank has been trimmed to length.
Rear center removed from the duplicator and tapped into the blank with a stout hammer.
Back to the duplicator. Using two levels to adjust the blank "on the level" with the pattern. In addition to the 3/8" cast off the pattern has 5/8" drop at the front of the comb, 1-3/4" drop at heel and 14-1/4" pull. The rifle is a dedicated iron sight rifle in 458 Lott, no scope, the stock is designed for easy line up of the sights.
Now for the "Run Around". 1/4" diameter rods in the spindles. I run the right hand rod all around the blank, while maintaining contact. If the left hand rod touches the pattern, the blank must be re adjusted or it is not thick enough. This procedure ensures that I have enough wood in the blank and will not be "cutting air".
Rotate the pattern and blank 90 degrees and run around again.
Now it is time to scribe lines for the band saw treatment. The right hand rod is replaced with a sharp scribe. Then the tracer spindle with the 1/4" rod is run around the pattern while maintaining contact of the scribe with the blank. This results in scribed lines 1/8" larger than the pattern.
Look close and you may see the scribed lines. The blank goes to the band saw to remove excess wood.
Back to the duplicator with less wood. Doing it this way is less time consuming than removing all the wood with the duplicator.
Roughing cuts. The cutter is a special bit made for the furniture industry. It really removes wood! Cutter is 3/4" diameter. This tracer stylus is teflon tipped for smooth sliding and is 1" in diameter. Combined with setting the cuter 1/8" higher than the tracer results in a carved stock that is 1/8" oversize.
Setting the cutter 1/8" higher than the tracer. A 1/8" thick shim is under the cutter and the tracer is adjusted to touch the leveling board.
After the first roughing cuts I put in a 7/8" diameter tracer and reset the cutter 1/16" higher than the tracer. This results in the stock being 1/16" oversize.
Then to a 1/32" shim and a 13/16" diameter tracer if I want to leave a 1/32" sanding allowance. Or a tracer the same size as the cutter and no shim if I want to go to exact size.
Cutter bits and tracers of various sizes for different areas of the stock. The T-Handle is for adjusting the spur center positions and also fits the tracer spindle. Carbide bits are standard router bits. The High Speed Steel bits are the special furniture industry roughing bits. I have many other cutter bits, the ones shown are the most used.
The below is a previous carve of a stock for a 40X in 22-250 Rem. Also Maple.
40X stock. Fresh off the duplicator and rough sanded no finish. That sanding cradle is real handy: It has the same centers as the duplicator, rotates 360 degrees and may be locked in any position. I clamp it in a big wood vise on the bench.
The plywood on the end will come off as it was screwed on to prevent splintering of the end of the stock.
Back to the first stock.
Another roughing view. 3/4" diameter cutter, 1/2" depth cut. The reason for big motors.
The big crank rotates the pattern and the blank. Spur centers for the pattern and blanks are linked to a common shaft via 90 degree worm gearing. You can see the carved stock is becoming smoother: Down to the finishing cuts.
Another view. Drilling the action screw holes. 1/4" diameter rod in the tracer spindle, 1/4" drill bit in the carving spindle.
Pattern:
Stock:
Woo Hoo! Look at the grain in the barrel channel. Looks like the grain on this one goes all the way through the wood. I left the top of the stock about 1/32" proud to allow for final sanding. Once the stock is finished with my special concoctions the grain will really pop and the overall color will be a little darker. There is also a little more work to do inside the action recess.
Here is what a good log looks like just under the bark. Those bumpty bumps tell the "WoodHunter" what may be waiting to be revealed at the sawmill. The sides of the blank have been planed to reveal the grain: Note the tiger stripes continuing from the bumps. Few trees have grain this good. This tree was about 4 feet in diameter.
At the sawmill. The knarlier the log is on the outside, the better chance of finding good grain inside. Look at all that green moss: This is Sasquatch Country in the Pacific North West.
A lot of plain grain boards and firewood is made when searching for that "Grain to Die For". Photo taken 21 years ago. The blanks from this log have been silently air curing.
Making the pattern stock. Bedding the barrel channel and front of the action to give a good hard surface for the tracer to follow.
Back view. That funny looking knob on the back of the tracing arm is an adjustable balance weight on a length of 1" all thread. Those big 220 volt motors have a lot of torque.
The blank is Pacific Big Leaf Maple with a 21 year air cure. 2-3/4" thick as the stock will have 3/8" cast off. The pattern is made from plain grain maple and painted with hard black epoxy paint for a slick tracing surface.

First thing is to layout the location for the duplicator centers. The rear is a spur center, front is a cupped center.
Center lines and a 3/8" offset for the cast off. The pattern was made with 3/8 cast off. Blank has been trimmed to length.
Rear center removed from the duplicator and tapped into the blank with a stout hammer.
Back to the duplicator. Using two levels to adjust the blank "on the level" with the pattern. In addition to the 3/8" cast off the pattern has 5/8" drop at the front of the comb, 1-3/4" drop at heel and 14-1/4" pull. The rifle is a dedicated iron sight rifle in 458 Lott, no scope, the stock is designed for easy line up of the sights.
Now for the "Run Around". 1/4" diameter rods in the spindles. I run the right hand rod all around the blank, while maintaining contact. If the left hand rod touches the pattern, the blank must be re adjusted or it is not thick enough. This procedure ensures that I have enough wood in the blank and will not be "cutting air".
Rotate the pattern and blank 90 degrees and run around again.
Now it is time to scribe lines for the band saw treatment. The right hand rod is replaced with a sharp scribe. Then the tracer spindle with the 1/4" rod is run around the pattern while maintaining contact of the scribe with the blank. This results in scribed lines 1/8" larger than the pattern.
Look close and you may see the scribed lines. The blank goes to the band saw to remove excess wood.
Back to the duplicator with less wood. Doing it this way is less time consuming than removing all the wood with the duplicator.
Roughing cuts. The cutter is a special bit made for the furniture industry. It really removes wood! Cutter is 3/4" diameter. This tracer stylus is teflon tipped for smooth sliding and is 1" in diameter. Combined with setting the cuter 1/8" higher than the tracer results in a carved stock that is 1/8" oversize.
Setting the cutter 1/8" higher than the tracer. A 1/8" thick shim is under the cutter and the tracer is adjusted to touch the leveling board.
After the first roughing cuts I put in a 7/8" diameter tracer and reset the cutter 1/16" higher than the tracer. This results in the stock being 1/16" oversize.
Then to a 1/32" shim and a 13/16" diameter tracer if I want to leave a 1/32" sanding allowance. Or a tracer the same size as the cutter and no shim if I want to go to exact size.
Cutter bits and tracers of various sizes for different areas of the stock. The T-Handle is for adjusting the spur center positions and also fits the tracer spindle. Carbide bits are standard router bits. The High Speed Steel bits are the special furniture industry roughing bits. I have many other cutter bits, the ones shown are the most used.
The below is a previous carve of a stock for a 40X in 22-250 Rem. Also Maple.
40X stock. Fresh off the duplicator and rough sanded no finish. That sanding cradle is real handy: It has the same centers as the duplicator, rotates 360 degrees and may be locked in any position. I clamp it in a big wood vise on the bench.
The plywood on the end will come off as it was screwed on to prevent splintering of the end of the stock.
Back to the first stock.
Another roughing view. 3/4" diameter cutter, 1/2" depth cut. The reason for big motors.
The big crank rotates the pattern and the blank. Spur centers for the pattern and blanks are linked to a common shaft via 90 degree worm gearing. You can see the carved stock is becoming smoother: Down to the finishing cuts.
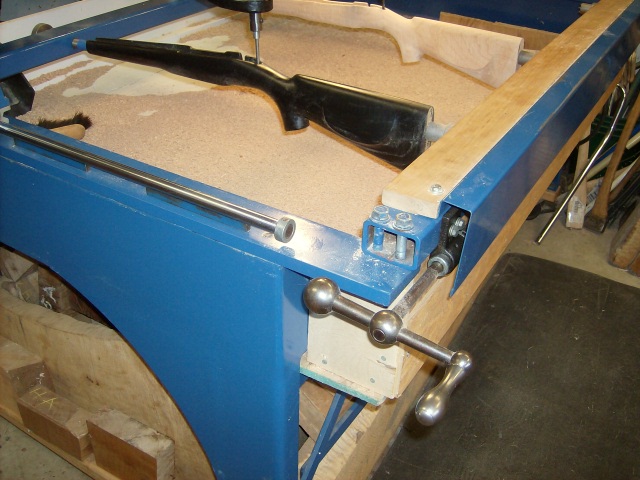
Another view. Drilling the action screw holes. 1/4" diameter rod in the tracer spindle, 1/4" drill bit in the carving spindle.

Pattern:
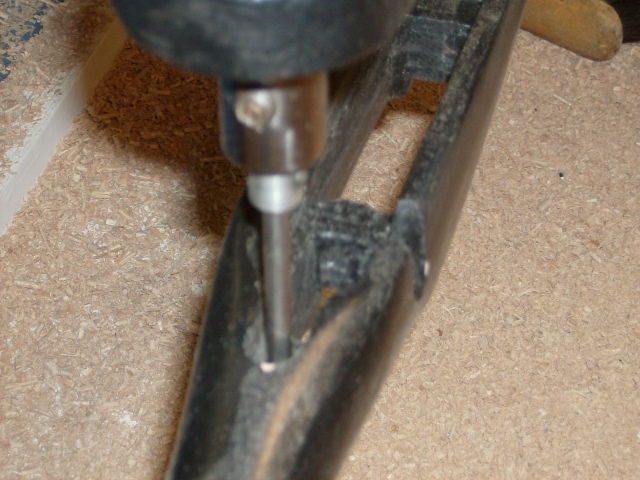
Stock:

Woo Hoo! Look at the grain in the barrel channel. Looks like the grain on this one goes all the way through the wood. I left the top of the stock about 1/32" proud to allow for final sanding. Once the stock is finished with my special concoctions the grain will really pop and the overall color will be a little darker. There is also a little more work to do inside the action recess.


Here is what a good log looks like just under the bark. Those bumpty bumps tell the "WoodHunter" what may be waiting to be revealed at the sawmill. The sides of the blank have been planed to reveal the grain: Note the tiger stripes continuing from the bumps. Few trees have grain this good. This tree was about 4 feet in diameter.
At the sawmill. The knarlier the log is on the outside, the better chance of finding good grain inside. Look at all that green moss: This is Sasquatch Country in the Pacific North West.
A lot of plain grain boards and firewood is made when searching for that "Grain to Die For". Photo taken 21 years ago. The blanks from this log have been silently air curing.
Making the pattern stock. Bedding the barrel channel and front of the action to give a good hard surface for the tracer to follow.
Attachments
-
2015-04-10 006.jpg134.3 KB · Views: 520
-
ry=400.jpeg26.8 KB · Views: 514
-
ry=400-8.jpeg23.8 KB · Views: 551
-
ry=400-13.jpeg24.6 KB · Views: 598
-
ry=400-9.jpeg26.6 KB · Views: 500
-
upload_2016-4-7_15-49-24.png209.7 KB · Views: 495
-
ry=400-12.jpeg33.6 KB · Views: 537
-
2015-04-10 004.jpg141 KB · Views: 513
-
ry=400-11.jpeg30.3 KB · Views: 744
-
ry=400-10.jpeg21.8 KB · Views: 525
-
2015-04-10 001.jpg139.4 KB · Views: 473
-
2015-04-10 003.jpg142 KB · Views: 551
-
2015-04-10 005.jpg135.3 KB · Views: 429
-
2000-12-31 021.jpg225.1 KB · Views: 1,055
-
ry=400-2.jpeg27.3 KB · Views: 507
-
ry=400-18.jpeg26.1 KB · Views: 530
-
ry=400-3.jpeg28.4 KB · Views: 466
-
ry=400-21.jpeg47.7 KB · Views: 488
-
ry=400-20.jpeg33.3 KB · Views: 499
-
ry=400-4.jpeg26.4 KB · Views: 470
-
ry=400-19.jpeg31.1 KB · Views: 417
-
ry=400-17.jpeg27.3 KB · Views: 516
-
ry=400-5.jpeg26.8 KB · Views: 448
-
ry=480.jpeg36.1 KB · Views: 477
-
ry=400-16.jpeg33 KB · Views: 502
-
ry=400-6.jpeg28.9 KB · Views: 610
-
ry=400-15.jpeg29.7 KB · Views: 564
-
ry=400-14.jpeg23.5 KB · Views: 453
-
ry=400-7.jpeg27.2 KB · Views: 494
-
2015-04-10 002.jpg135 KB · Views: 516
Last edited by a moderator: